This semester our goals were to redesign our landing gear and empennage, begin fabrication of a control wing, continue the parametric design project, research the next configuration of wings, and conduct our second flight with the truss-braced wings.
The Redesigned Landing Gear & Empennage :
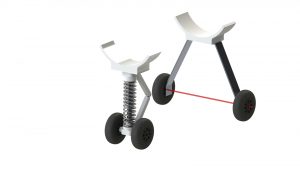
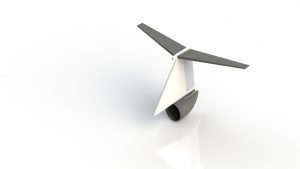
The Build Team redesigned the landing gear. In Spring 2021 we utilized a taildragger setup. This semester we opted to go for a tricycle system with the front gear being a spring-loaded landing gear mounted next to the nose of the fuselage. The empennage was also sized up to provide better movement using the rudder and elevators. We also cut out and installed flaps to the truss-braced wing and cut out a bay door for easier electronic management. The model of the full aircraft is shown below.
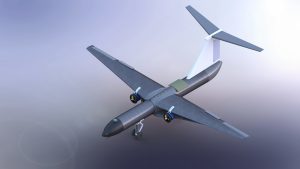
The Parametric Design Project:
We continued the parametric design project and finished the first step of the code. By our technical advisors’ suggestions, we will be moving into parametric sizing next semester. The current code provides dimensions for an empennage using the moment arm from the wings. The parametric sizing code is will allow us to more freely experiment with wing and empennage sizes, as well as using different empennage configurations.
A Shift with the Cantilever Control Wing:
We originally decided to construct a new wing based on the Boeing 737’s wing using the same build as the truss-braced wing. However, we decided mid-semester to do a shift and to focus on the control wing due to issues we had with the current truss-braced wing. We decided to order a Freewing AL37 RC Aircraft from MotionRC to simplify this work and allow us to reverse-engineer components like the landing gear and various control surfaces in future semesters.
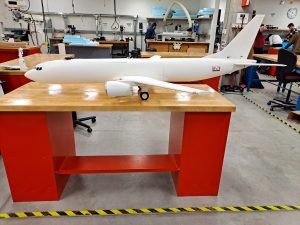
The aircraft will allow us to gather aircraft performance data that can be compared to known data from the Boeing 737 & 737 MAX. The aircraft is 6.51 ft long from nose-tip to tail-tip and 6 ft in wingspan from wingtip to wingtip. The truss-braced wing build was roughly 6 ft long from nose-tip to tail-tip and 7.39 ft in wingspan tip-to-tip.
Next Generation of Wings & The Truss-Braced Wing’s Future:
We researched more wing configurations, from the Prandtl box wing to delta wings, among others. We are also looking to improve the truss-braced wing next semester. We will select a more efficient airfoil and create a set of truss-braced wings using the AL37 fuselage as our base for testing. The AL37 manual contains several drawings that we can reproduce in Solidworks, which will allow us to reverse-engineer the wings and tweak the fuselage while keeping the same landing gear. We can also revisit the T-Tail for comparison with the AL37 wings. Once these tests are done, we will begin to compose a full report on the truss-braced wing to send to Boeing, and continue to work on the design with the carbon-fiber build.
Documentation Methods:
Over the course of the semester, we found issues that were due to a lack of sufficient documentation in previous semesters. We have decided to fix this issue by incorporating more documentation methods and templates using LaTeX and GitHub to keep our work well documented and in an easy-to-access point. This will lower the risk of double researching wing configurations or losing information about the aircraft.
Closing Semester Thoughts:
We learned many things this semester about the aircraft design process, as well as practices that become increasingly important in projects and in the industry. We found ourselves with some issues due to lack of documentation and flawed designs that we continuously tried to fix with little experience or knowledge about the designs themselves. This semester allowed us to establish a ground set of documentation practices and further study what we did right this semester and what we can improve upon next semester. A Gantt chart of the project this semester can be observed below.
For the immediate future, we will be revisiting the truss-braced wing design to continue working on that project, using the AL37 fuselage and retractable landing gears as a base. We can then reverse-engineer those features onto the carbon fiber build. We will continue to expand on the parametric design project. We will continue to utilize the AL37 to conduct more test flights to gather more data and to experiment with the Pixhawk further.
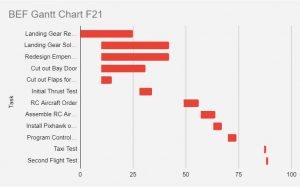