The MAVRIC Mechanical Team is responsible for designing, manufacturing, and testing all mechanical and electromechanical systems on the rover. This includes major subsystems such as the rover’s chassis, suspension, robotic arm, and other considerations like camera and radio mounting. The Mechanical Team also ensures the rover remains under the 50-kilogram mass limit imposed by URC. The main goal of the Mechanical Team is to create a competition-suitable rover that will remain mechanically sound through all of the competition tasks.
Members:
- Tyler Schmitz– Team Lead
- Nick Faith
- Sam Jahnke
- Daniel Minchew
- Kyler Nielsen
- Sam Schwartz
From left to right: Samuel Schwartz, Kyler Neilsen, David Minchew, Nick Faith, Tyler Schmitz, Sam Jahnke
Goals:
Our main goal is to complete a competition ready science system. The science system will use ATP luminometry and protein detection swabs from Hygiena to detect for extant and extinct signs of life. Another goal is to complete thorough testing of the rover’s mechanical systems, probably involving minor updates to the arm and drivetrain.
Deliverables:
Our deliverable this semester is the redesign and manufacture of the science system. It must be capable of detecting signs of life and collecting a soil sample.
Milestones:
-
- Science system prototype created (March 3rd)
- Science system completed (May 5th)
Spring 2023 Progress:
This semester, we have completed our goal of a science system prototype. This is shown below. The science system is currently being updated to improve the operation of the systems, as we found many issues with the system as it is constructed. Since we were not admitted to competition, we are no longer pressured to have the rover in a perfectly operational condition at the end of the semester. We have been focusing on updating many minor assemblies that have needed work for some time but have not been a high priority. We are also looking at upgrading the wrist system.
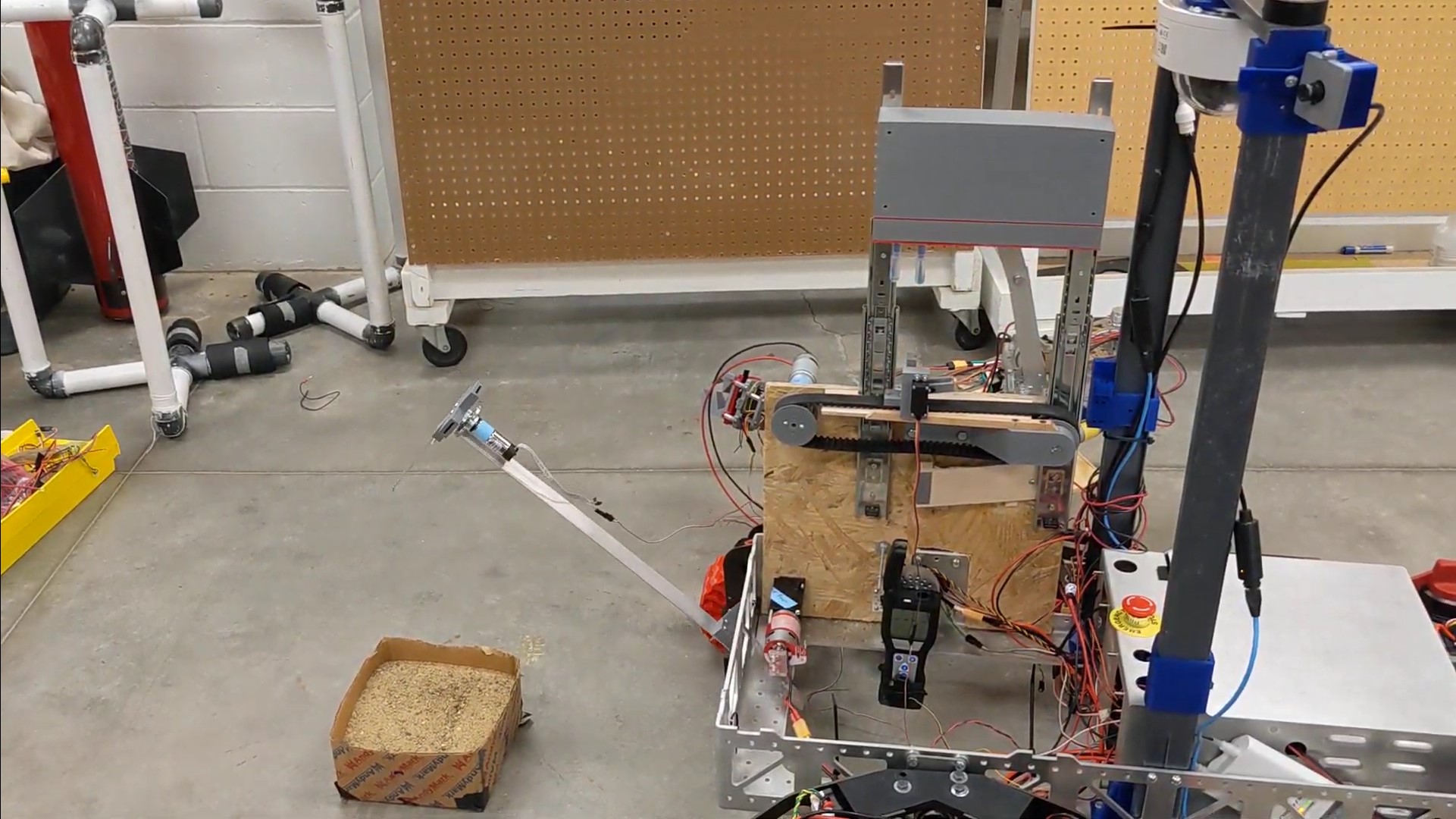
Fall 2022 Progress:
This semester we have completely redesigned our suspension system. With the exception of maintaining the functionality and design principles of the old system, the new system was designed from scratch. It massively improves the structural soundness of the suspension members while reducing the assembly’s weight. The new system is also more capable than the old suspension by virtue of using brushless motors instead of brushed motors and increasing the wheel diameter and width to assist with terrain navigation. The suspension system has been completely designed, and most of the components are either produced or in production. We have completed the assembly of one suspension fork, which allows us to prove that the new system is better than the old one. We still believe that the suspension system can be completed by the end of the semester.

Our other main focus this semester has been on the shoulder and wrist assemblies of the arm. The shoulder has been completely redesigned to improve controllability, reduce the play in the system, and reduce the weight. The new system has been completely designed, and most of the parts have had prototypes produced, but we are waiting on finalized parts to complete the assembly. The wrist design was updated to allow us to use motors with a lower RPM and higher torque, which will help with controllability and allow us some additional strength for manipulating controls in the field. The design has been updated to include a slip ring in the wrist assembly, allowing us to rotate the end effector indefinitely. The end effector has also been updated with a better set of fingers that are more versatile and better suited for the challenges we faced back in June. The end effector system has been completely prototyped, and only a few minor changes need to be completed for the system to be competition ready.

