First row (Left to Right): William Coloff, Advaith Thimmancherla, Mason Lubben, Valeria Medina, Logan Shelby, Aiden Schueler
Second row (Left to Right): Cowles Anderson, Timothy Texley, Enrique Campos, Paiden Nicks, Logan Castle, Nicholas McCormick, James Burke, Eli Schmitt
Hierarchy
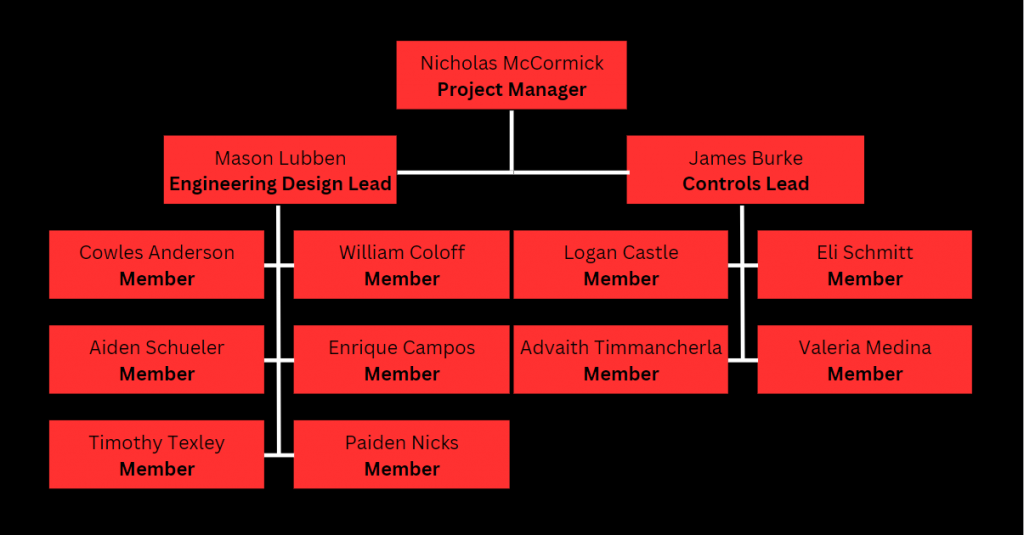
Subteams
Engineering Design
Team Goals
The goals of the Engineering design team this semester are to test the injector at a flowrate of 1 kg/s and create a better chamber and nozzle design so that it can fit in the metal 3D printer.
Team Milestones
- Create a test plan for injector testing
- Generate chamber inner wall using Rao Nozzle Approximation
- Design and print new pintle tip design using ABS
- Perform Injector Tests
- Write report on Injector Tests
- Integrate regenerative cooling channels with chamber and nozzle
- Print Chamber and Nozzle using PLA
- *Not Started*, *In Progress*, *Complete*
Team Spring 2023 Update
The Engineering Design team has worked on preparing to conduct cold flow injector testing using a full flow rate of 1 kg/s of water. The team need to design a test set up and create multiple new pintle injector tip designs to test and compare using Particle Image Velocimetry (PIV) analysis techniques.
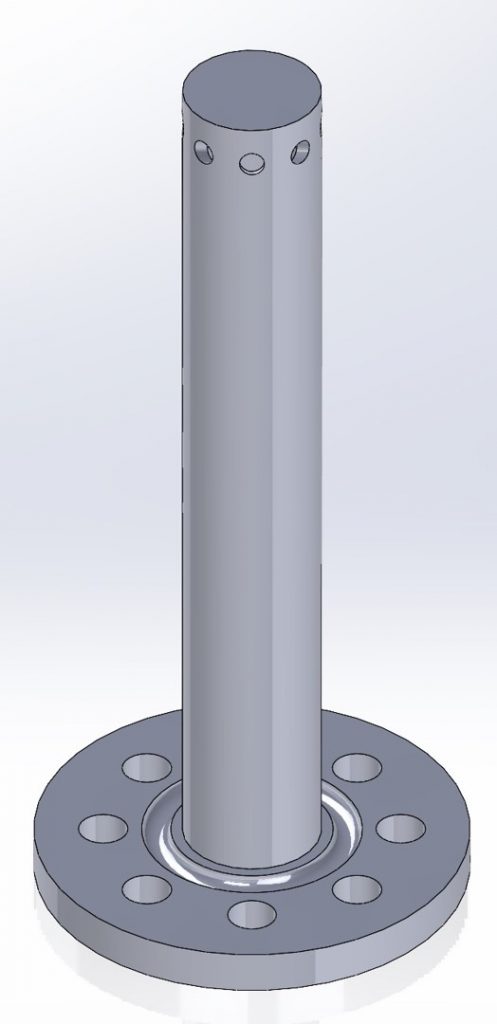
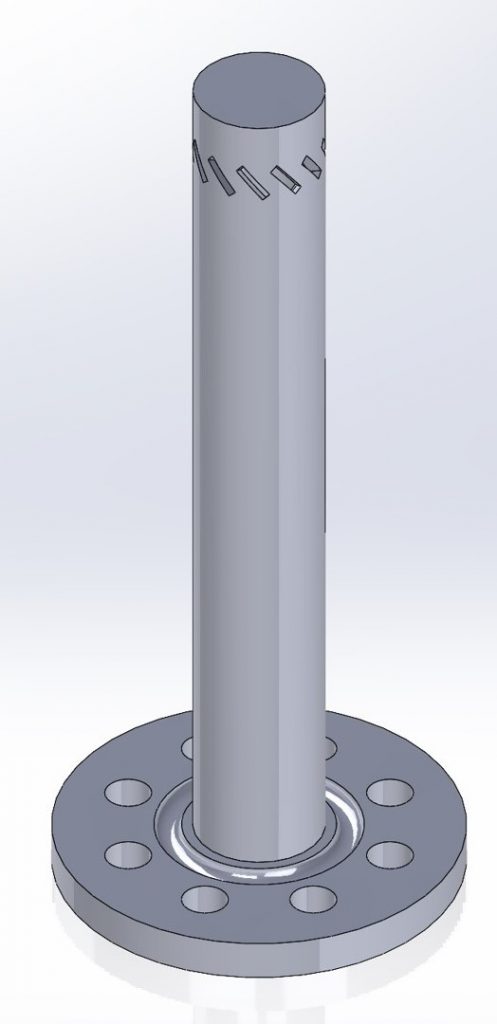
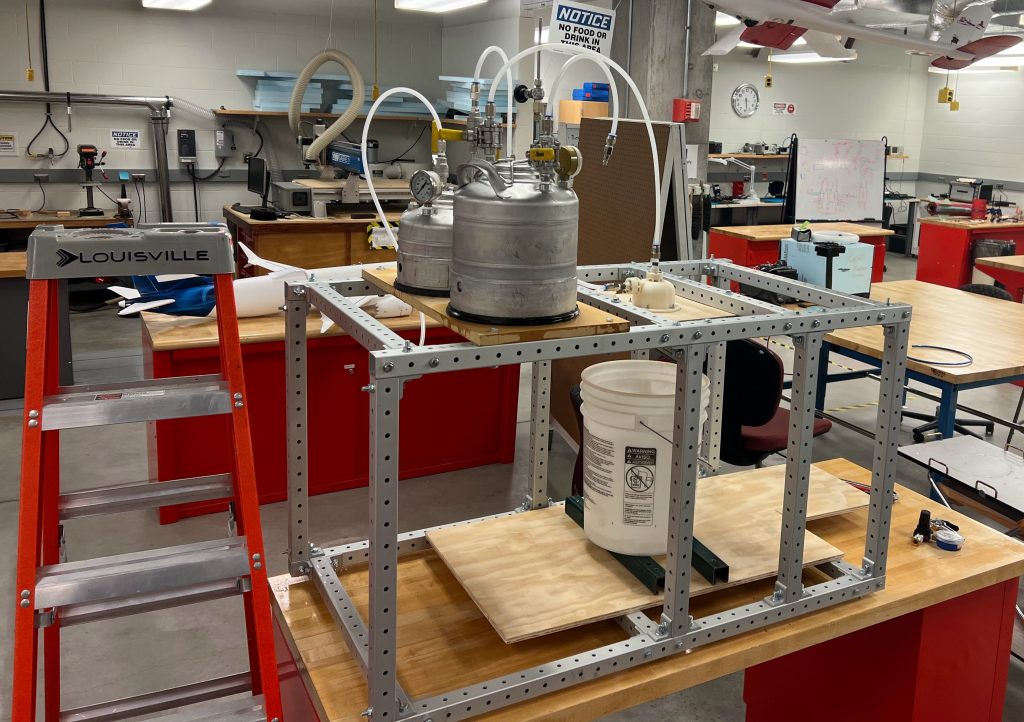
The Engineering Design Team has also been working on the redesign of the thrust chamber and nozzle design, including the implementation of accurate regenerative cooling channels. The new chamber and nozzle design used the Rao Nozzle geometry which is 80% the length of the characteristic nozzle geometry. The change in length reduces the weight of the engines and allows us to use the metal 3D printer here at Iowa State University, which we will need to use when hot fire testing is conducted in the future (Hot fire testing has not been conducted, and flammable or combustible.
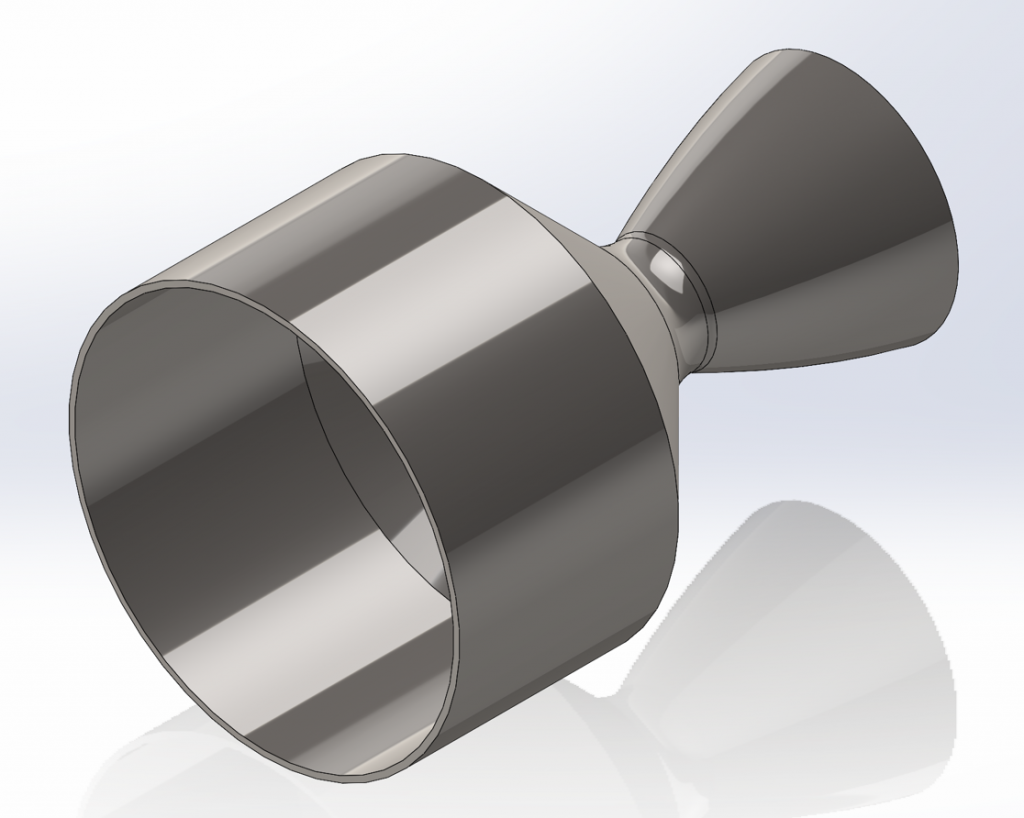
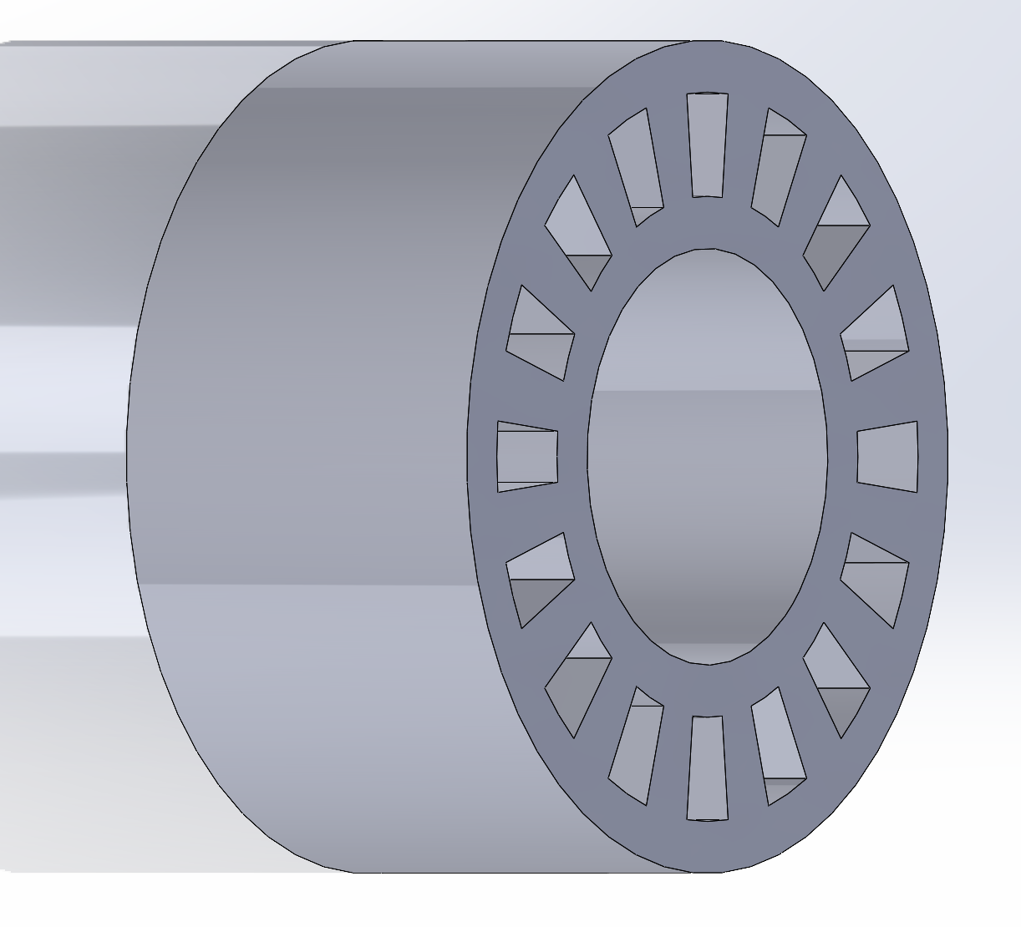
For the remainder of the semester, the Design team will work on finalizing and printing the new nozzle and combustion chamber, generating methodology documentation on the design for the regenerative cooling, and analyzing the injector test data.
Controls Team
Team Goals
The goals of the Controls team this semester are to write reports to help determine what pressure vessels and cryogenic hardware we should buy in the future. Another goal this semester is to construct and integrate the first half of the fuel side of the fluid feed system in Stellar’s test stand “Pathfinder” with LabView.
Team Milestones
- Research Pressure Vessels
- Research Cryogenic Hardware
- Write a report and recommendation on Pressure Vessels
- Write a report and recommendation on Cryogenic Hardware
- Order remaining parts for the fluid feed system
- Write Labview code to control and get data from the fluid feed system
- Assemble the fluid feed system.
- Integrate fluid feed system with LabView
- *Not Started*, *In Progress*, *Complete*
Team Spring 2023 Update
In the first half of the semester the Controls team worked on researching cryogenic hardware, and pressure vessels. The documents include what specifications we require for our project, and contain a list of potential items that would work, and a final list of the recommended components.
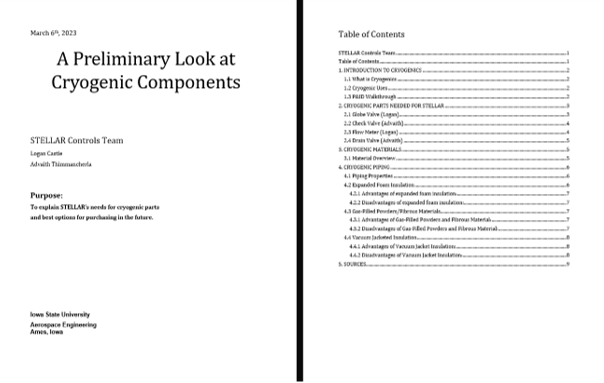
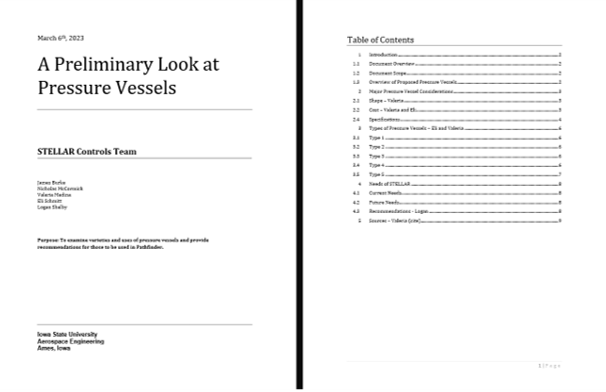
Recently the controls team has been working on assembling the fluid feed system with parts we ordered this semester and the past few semesters. In addition to assembly, the Controls team has also been integrating the hardware within LabView to make testing and data collection easier.
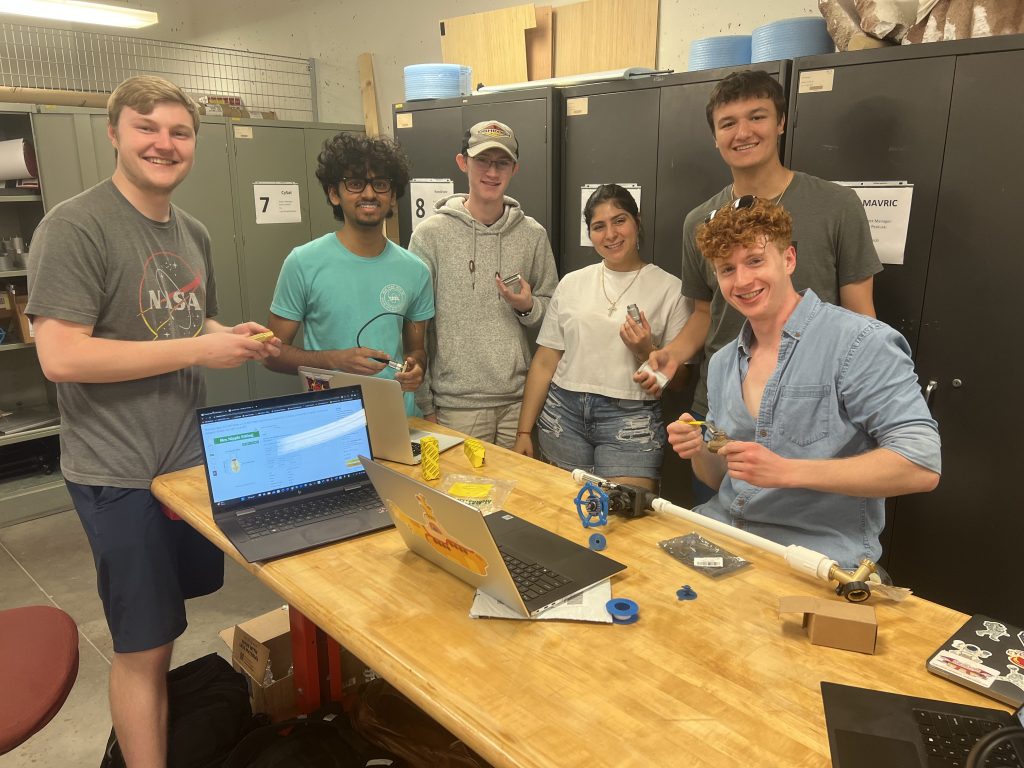
For the rest of the semester, the controls team will be focussing on determining the time needed to run the stepper motor to fully open and close the globe valve, developing an early-stage new LabView code that is more user-friendly than the previous version, and assembling a single flow line onto Pathfinder Test Stand with stepper-motor-globe-valve control and pressure-reading-capability.