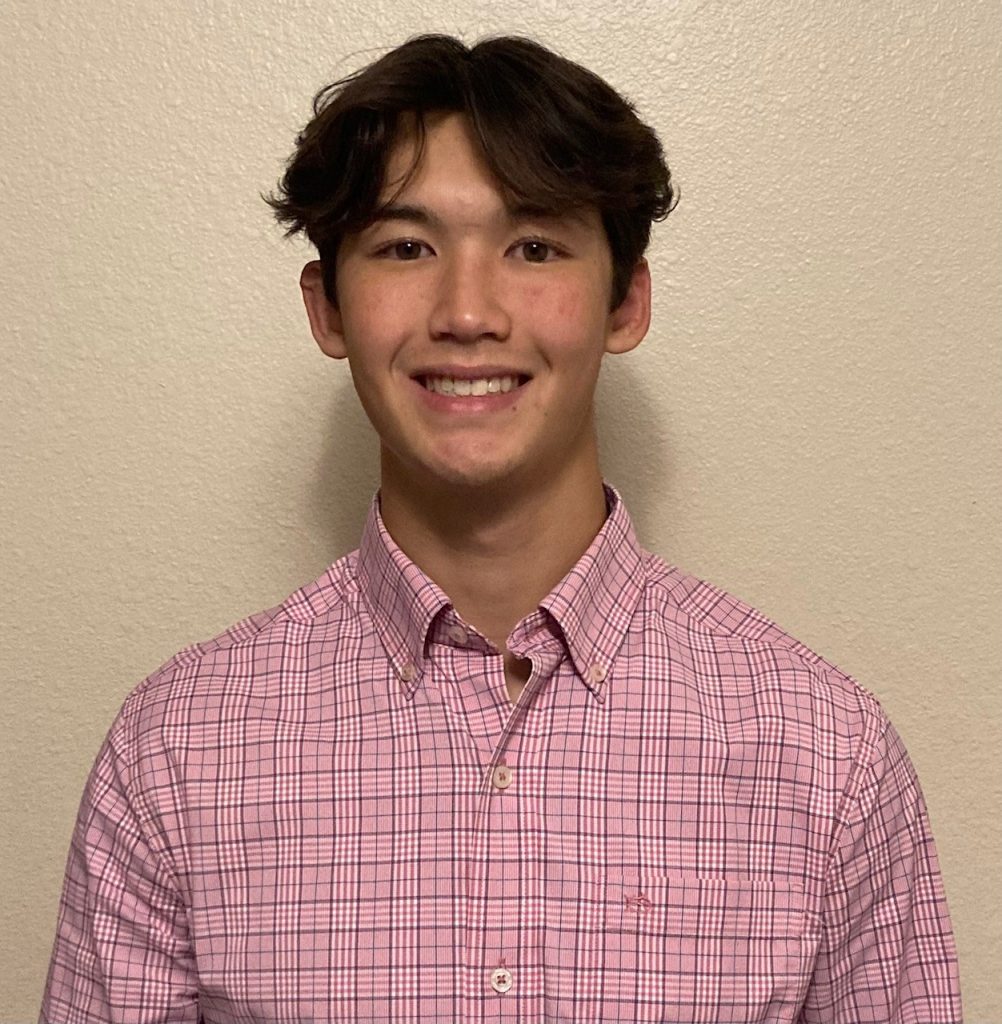
Mechanical Team Lead: Ben Nguy
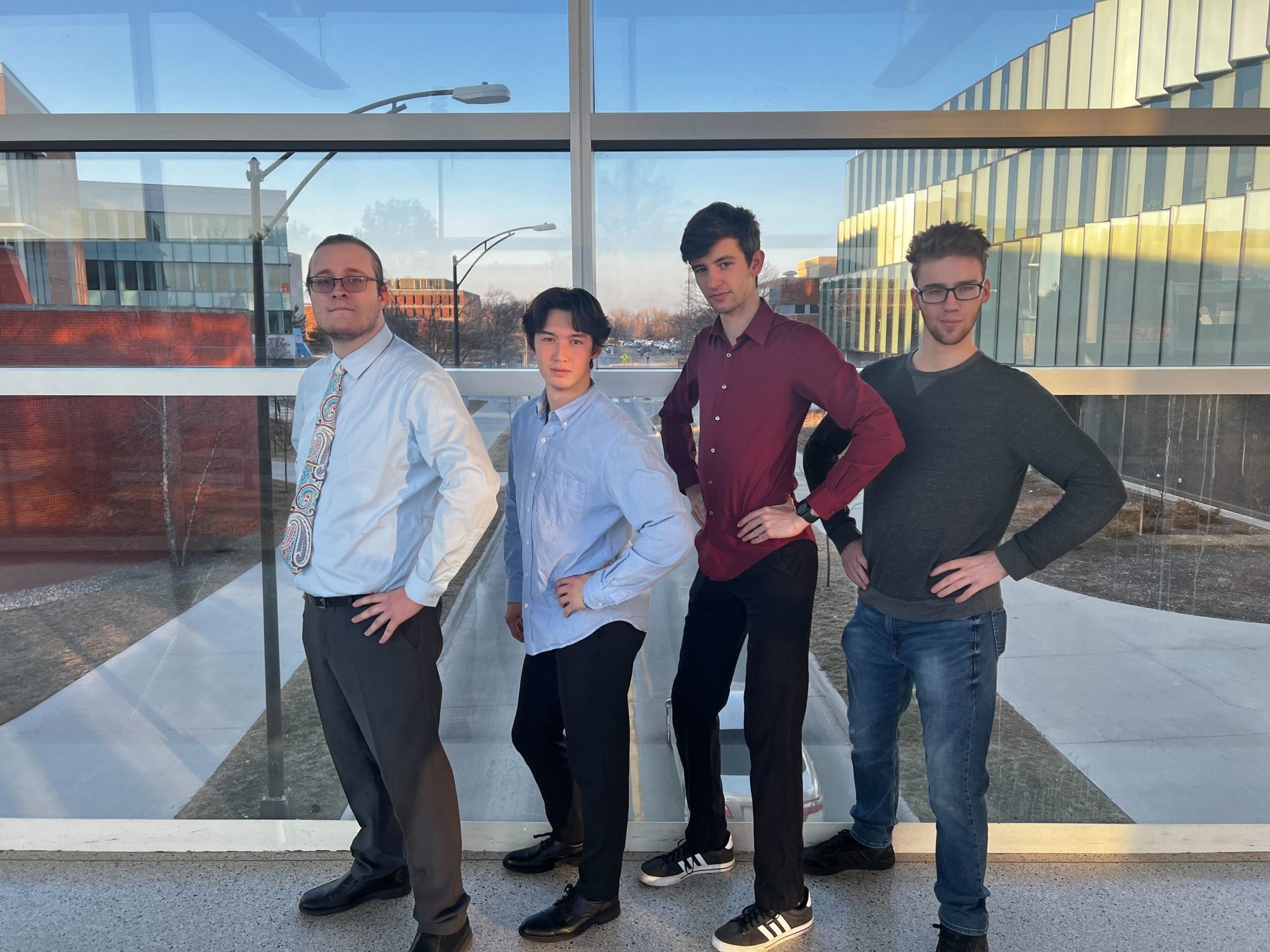
Evan Charlier, Joel Todden, Adam Everhardt, and Ben Nguy
Team Goals
- Design and manufacture a search and rescue robot capable of overcoming numerous obstacles and terrains
- Create a chassis to house all of the necessary components while being resilient
- Create four independent flippers with treads to drive the robot and can also rotate freely
Fall Semester 2022 Deliverables
- Have a working prototype of a robot flipper that is able to rotate +-90 degrees and move a tread five revolutions
- Have a completed CAD model of the robot chassis with accurate dimensions and documentation.
Spring semester 2023 deliverables
- Constructed chassis with 4 rigidly connected flippers on parallel sides.
- Constructed arm with at least 4 degrees of freedom.
Milestones
- Complete CAD of arm
- Full CAD model of chassis, flippers, camera mounts, and arm
- Constructed chassis with four flippers attached
- Constructed Arm, mounted to the chassis
- Ready to test in simulated environment
Fall 2022 Progress report
- We have a completed cad model in SolidWorks of the robot using accurate dimensions
- One flipper is constructed and ready for testing
- Assembled Chassis
This semester our goals were to complete a cad model of our chassis with real life dimensions in order to create a prototype. Additionally, we aimed to machine and assemble the parts for the robot prototype and create a flipper that is able to rotate + – 90 degrees and move the tread five revolutions. So far, we have most of this accomplished. We have finished the cad model necessary to create a prototype for this semester, which uses accurate dimensions and includes the motors and gearboxes for the flippers. We have also completely machined and assembled the chassis, which includes the frame, belly pan, and gusset plates. Finally, we fully constructed one flipper that is ready to be hooked up to a motor and tested.
Spring 2023 Progress report
- Completed updated Chassis machining and assembly
- Completed machining and construction of the four flippers
- Arm design completed with torque math
This semester our goals were to completely construct the chassis with 4 flippers being rigidly attached and to construct an arm with at least 4 degrees of freedom. Our first deliverable was completed in early march but we have struck issues with the flipper treads being very tight and causing problems for our Neo-550 motors. Most of these problems have been reduced by altering the number of teeth on the front flipper gears, and by updating the tread spacers to reduce friction on the frame. Additionally, to complete the first deliverable, we updated the design of the chassis rails that made the flipper connections more user friendly by allowing easy access to the hex shaft couplers. The second deliverable is in late production and will be accomplished very soon, as the design has already been completed and approved, and manufacturing has begun, one degree of freedom at a time. We currently have the arm base completely manufactured, with the shoulder being finished up this week (4/14), and the wrist connection being (optimistically) finished in the next two weeks.
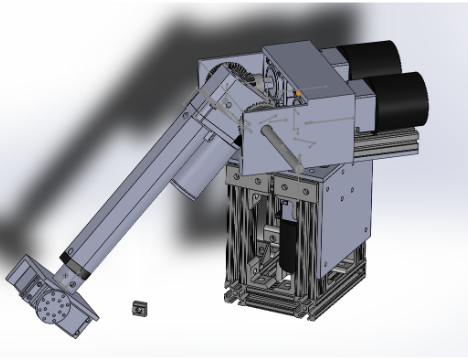
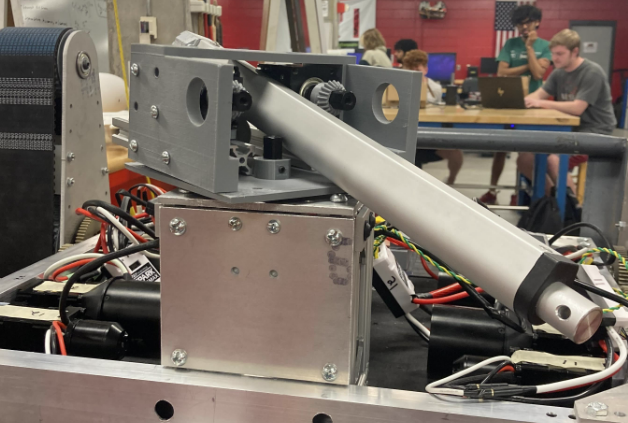
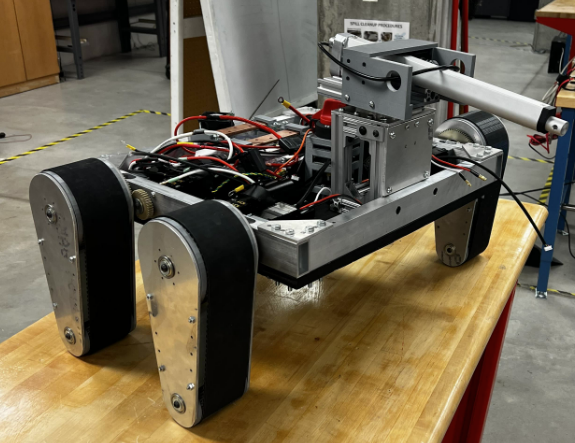